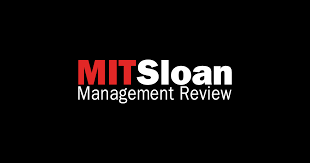
Weekly Business Insights from Top Ten Business Magazines
Week 321 |Shaping Section | 4
Extractive summaries and key takeaways from the articles curated from TOP TEN BUSINESS MAGAZINES to promote informed business decision-making | Since September 2017 | Week 321 | November 3-9, 2023

A Reshoring Renaissance Is Underway
By Erin McLaughlin and Dana M. Peterson | MIT Sloan Management Review | November 02, 2023
Extractive Summary of the Article | Listen
Companies are building manufacturing facilities in the U.S. at a pace not seen in decades. A confluence of factors is driving this trend: Amid supply chain bottlenecks, rising labor and transportation costs, U.S. tariffs on China, and geopolitical tensions, companies recognize the value of reshoring production. U.S. industrial policies favoring domestic manufacturing are also informing these decisions, including new laws seeking to address national security threats, economic disruptions, and dwindling access to key technological components. The result is an early-stage U.S. reshoring renaissance.
The reshoring renaissance does not apply universally. Sectors requiring large amounts of manual labor, including shoes and apparel, furniture, and home decorative items, are less likely to reshore. Industries with more complex and expensive products, and those that can use automation and robotics in manufacturing, are leading the U.S. resurgence. The five industries experiencing the greatest U.S. employment growth as a result of reshoring and direct investment are electrical equipment, appliances, and components; computer and electronic products; chemicals; transportation equipment; and medical equipment and supplies.
Business leaders should consider six key factors in deciding whether to adopt this model.
- Labor costs. Global labor shortages and cost increases — including in China, where wages are rising — make it relatively more affordable to locate manufacturing in the U.S. than it once was.
- Advanced manufacturing. New automated “smart factories,” which require more engineers and skilled technicians but often far fewer workers overall, including traditional assembly-line workers, make the U.S. labor pool attractive due to its well-educated workforce. Demand for robotics and the advanced technology that supports smart facilities is also surging.
- Risk mitigation. The longer and more complex the supply chain, the greater the risks it faces, especially in terms of potential geopolitical instability. There is also renewed scrutiny by the federal government of its own reliance on other economies for critical public health and national defense supplies and components, such as personal protective equipment and semiconductors used in military vehicles and weaponry.
- Sustainability With companies increasingly needing to meet sustainability goals and reduce their carbon footprints, localizing manufacturing offers several benefits. Constructing new, green facilities domestically can greatly reduce Scope 1 operating emissions from company-owned facilities and vehicles. Plus, manufacturing a product closer to its end customer reduces emissions from transportation.
- Stakeholder sentiment. Many companies’ stakeholders — including employees, corporate boards, industry organizations, government officials, and other companies connected within a supply chain — want executives to consider localizing manufacturing operations.
- Transportation costs. When deciding whether to onshore manufacturing operations, executives should weigh the benefits of lower international labor and operating costs against the greater cost of ocean freight shipping. Trans-Pacific shipping costs increased fifteenfold in 2021 from January 2020 levels, and while transportation costs have declined as the economy has slowed, the supply chain volatility of the last few years is front of mind for managers.
3 key takeaways from the article
- Companies are building manufacturing facilities in the U.S. at a pace not seen in decades. A confluence of factors is driving this trend: Amid supply chain bottlenecks, rising labor and transportation costs, U.S. tariffs on China, and geopolitical tensions, companies recognize the value of reshoring production. U.S. industrial policies favoring domestic manufacturing are also informing these decisions, including new laws seeking to address national security threats, economic disruptions, and dwindling access to key technological components. The result is an early-stage U.S. reshoring renaissance.
- The reshoring renaissance does not apply universally. Sectors requiring large amounts of manual labor, including shoes and apparel, furniture, and home decorative items, are less likely to reshore. Industries with more complex and expensive products, and those that can use automation and robotics in manufacturing, are leading the U.S. resurgence.
- The five industries experiencing the greatest U.S. employment growth as a result of reshoring and direct investment are electrical equipment, appliances, and components; computer and electronic products; chemicals; transportation equipment; and medical equipment and supplies.
(Copyright lies with the publisher)
Topics: Industrial Policies, Manufacturing, Reshoring, USA